Deconstructing the conditions that influence the supply chain
The inefficiencies of our global supply chain is a topic of discussion every day for us. It’s relevant to the entire world, and we recognize the need to have more conversations about it. We’ll start by sharing some insights we gleaned in conversation with our VP of Business Development, Anthony Perrella, and VP of Operations, Peter Perrella. When it comes to preventing the next supply chain crisis, it’s helpful to look at what caused the last one.
Wanting it today and transactional
Much of the supply chain is driven by transactional relationships between clients, carriers, and suppliers. Companies are looking for the lowest rates to accomplish their short-term goals, and carriers and suppliers price themselves accordingly to secure the contract. Understandably, everyone is concerned with the bottom line, but it’s a narrow focus on the short-term cost-efficiency that prevents us from unlocking greater value in the long run.
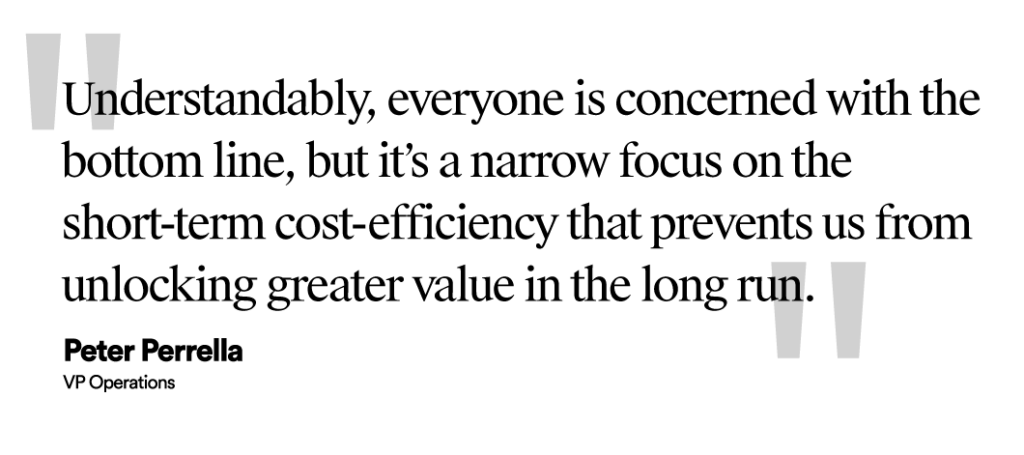
Where you see logistics providers often bidding on annual or 6-month RFPs, we recognize that, when thinking transactionally, your relationship is only as good as the rate. As a logistics provider whose business model is heavily built around relationships, our goal is to spend more time focusing on how we can become more efficient for our clients; how we do more with less? That in itself brings more value to the dynamic, and less costs to our clients’ business and operations, while allowing us to continue establishing longer-term relationships and a deeper understanding of how to increase efficiencies.
Fewer drivers by the day
Truck drivers represent 46% of the logistics and transport workforce, and the truck transportation industry has the second highest vacancy rate among Canadian industries, according to Trucking HR Canada.
The industry has already suffered from a lack of drivers for years, but it’s a trend that doesn’t seem like it’s about to change. In fact, it’s getting exponentially worse, year over year. Between 2019-2023 27,000 drivers will leave their jobs and an additional 7,200 will retire, according to Statistics Canada’s Job Vacancy and Wage Survey. The American Trucker Association (ATA) indicates that the truck driver shortage hit a historic high in 2021, and that shortage could double by 2030.
Factors behind the shortage include an aging workforce, difficulties attracting women and youth, and a high rate of voluntary turnover. Every year a driver goes into retirement, that’s another one who doesn’t get replaced. ATA estimates that over the next decade, the industry will have to recruit nearly 1,000,000 new drivers into the industry to replace drivers who’ve retired or left their occupation.
When you combine this dwindling interest in the role with an increase in demand across the supply chain, the need for drivers is that much greater. Despite the lack of interest from the younger members of the workforce, there needs to be a solution, because without drivers, everything grinds to a halt.
Trouble in the making
Companies looking to save costs will reduce production demands, which creates a “just in time” approach, whereby products are only created once they’re demanded. This creates a huge backlog of orders for materials, which in turn causes delays across the entire supply chain. We’ve seen this across various sectors, including food & beverage and pulp & paper. Unfortunately, this approach no longer applies or works with today’s demands and supply chain. Instead, we need to find new solutions. We need to look at new options that align with the new realities of the supply chain and meet consumer demands; adapting to new ways to shift the market to be ahead of the production line, ensuring there is enough product to support consumer needs.
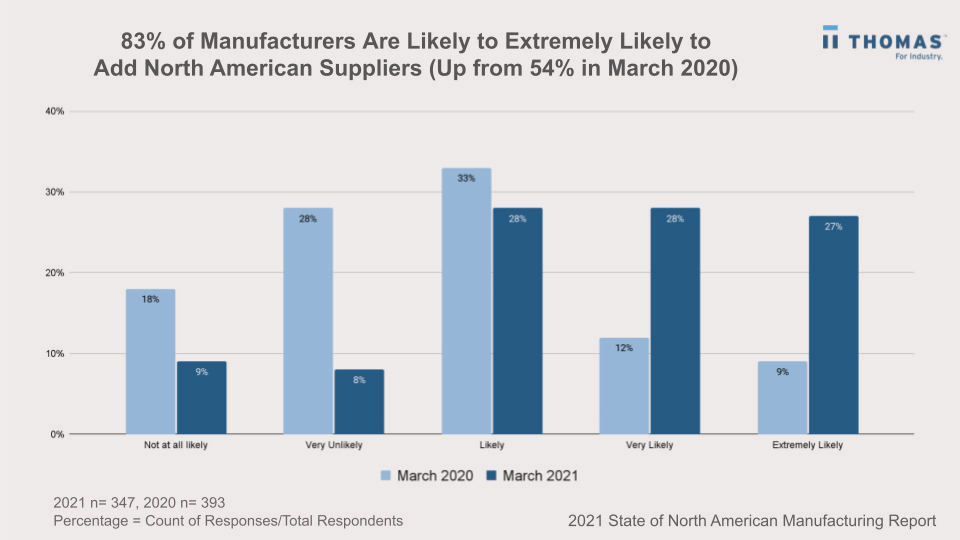
One study conducted by Thomas revealed that 94% of manufacturers surveyed listed ‘availability’ and ‘lead times’ as the most important factors when vetting new suppliers, instead of the generally anticipated answer ‘price per unit’. One respondent commented, “We need more U.S. manufacturers and the supply chain needs to be strengthened. Just-in-time does not work in a boom.”
What’s more, the majority of manufacturing is still done overseas, which certainly impacts how efficiently a product gets from A to B. This reliance has also seen widespread port congestion extend lead times longer than the industry’s seen, adding to issues with production and inventory. 83% of North American manufacturers are likely or extremely likely to reshore (up from 54% in March 2020). And if these manufacturers bring on just one single-contract domestic supplier, the shift would drive as much as $443 billion in U.S. economic value.
This increase in reshoring is a big reason why we’ve expanded our warehouse footprint, including our new warehouse in Brampton, one of North America’s largest logistics hubs. The more production we can move closer to home, the more opportunities we have to increase efficiencies exponentially.
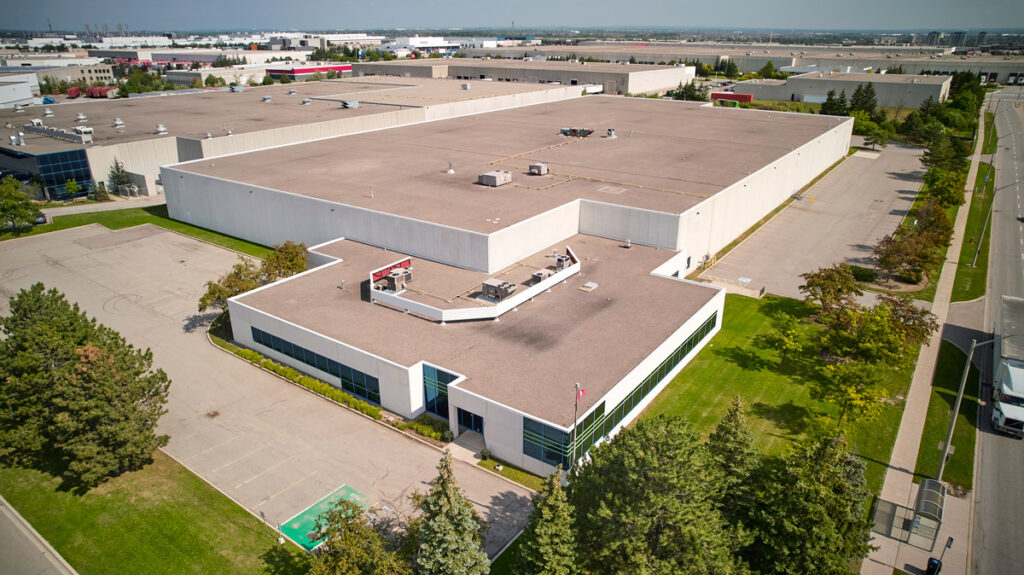
Not knowing what we don’t know
A big culprit of supply chain inefficiencies is the unknown. What will happen down the road? Trade wars, world wars, inflation… all of these variables impact the supply chain, and even with all of the forecasting tools, we don’t have a crystal ball to tell us what will happen next.
As one example, The Wall Street Journal reports that Russia’s invasion of Ukraine will cost the global economy $2.8 trillion in lost output by the end of next year. In its latest forecasts, the Organization for Economic Cooperation and Development (OECD) said the global economy was set to grow by 3% this year and 2.2% next year. Before the war, it had expected growth of 4.5% in 2022 and 3.2% in 2023.
There are also the cycles of the supply chain, which are becoming less predictable. The trends that we’ve seen in the past that were of a more seasonal nature, we are often seeing in more condensed timeframes, showing more volatility and faster swings. Driven by pandemic consumer demand and bottlenecked materials and ports, trucking costs rose 36% year over year in 2021, according to Bloomberg. As these issues persist, another 30% increase is expected for the trucking industry in 2022, while consumer prices may increase upwards of 10%.
The impact of world events on the supply chain will always be a reality. The question is, how can we stay prepared for unexpected variables, and mitigate some of these widespread consequences?
A feeling of helplessness (for now)
People’s outlook on the supply chain isn’t great. 75% of companies felt negative or strongly negative impacts on their business due to supply chain disruption, and 82% of people have concerns that the supply chain will ruin life plans like birthdays, vacations, holidays, and the purchasing of necessary items.
The supply chain has its issues, but what’s encouraging is that many of the solutions come down to one thing: communication. The better we understand the needs of customers, the more prepared we are to provide steady and reliable capacity. If all of us – logistics providers, clients, carriers, suppliers – increase how much and how often we communicate, we could really strengthen our supply chain to a degree we’ve never seen before. We just need to talk more, strategize more, and rethink how this entire system operates.
Stay tuned for our next installment of Rethinking the Supply Chain: More Conversations, More Often.
Sources: